
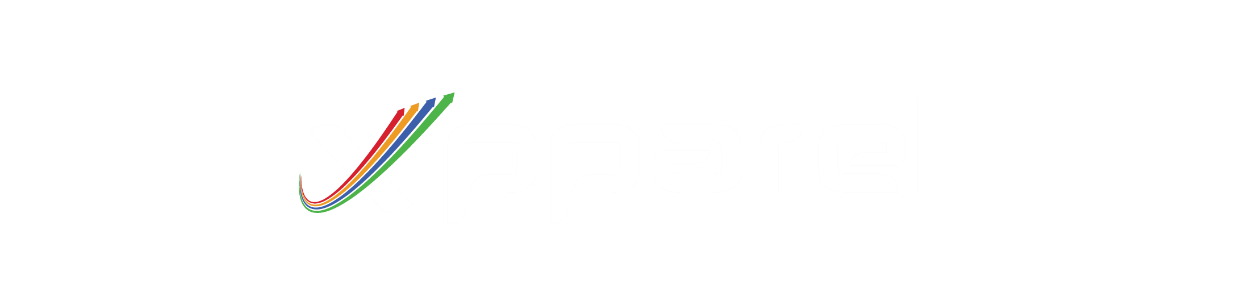
End
to end digital platform for apparel manufacturing
An End-to-End solution that handles from order receiving to dispatch with the entire production life cycle,
from raw material warehouse to logistic dispatch.
Business Benefits
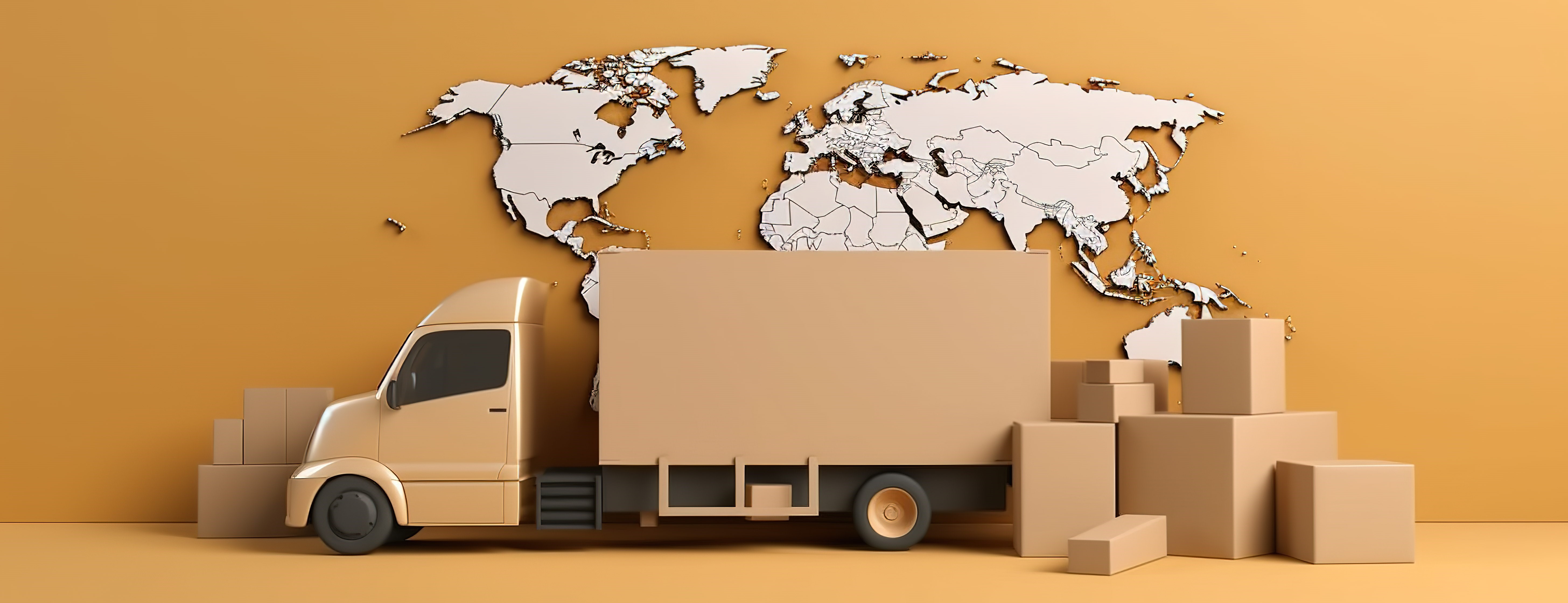
On Time Delivery
Advanced planning and scheduling capabilities, allowing
apparel
manufacturers to create optimal production schedules that consider various constraints and demand
forecasts
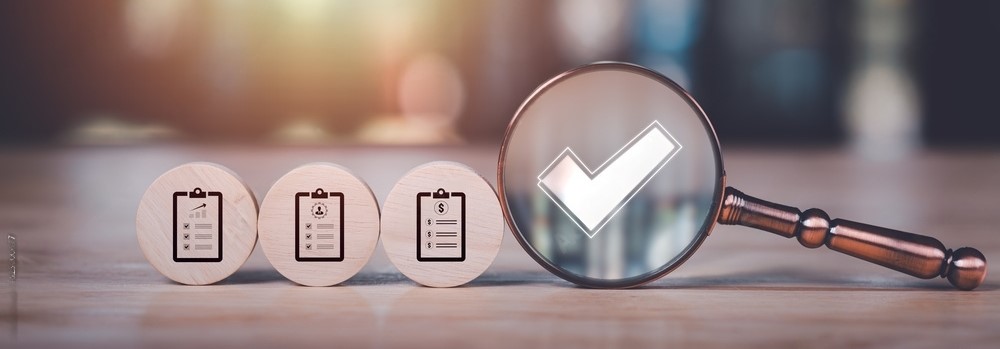
Quality Assurance
Buyer wise standard, Defect Capturing & rectification
measures,
Re-work process & Quality dashboard
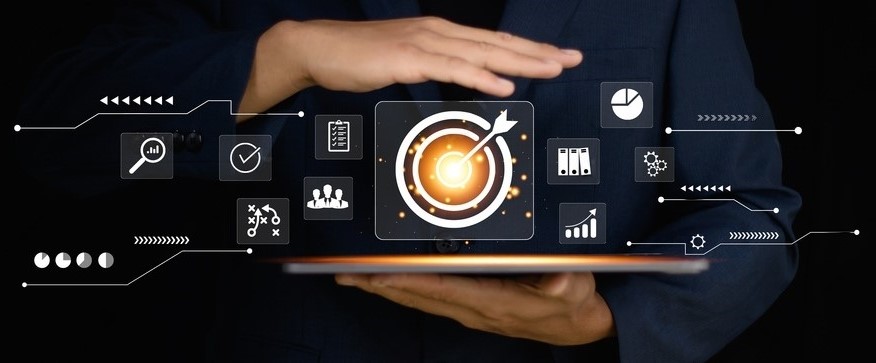
Resource Planning
Upgrading & Maintaining skill matrix, HRMS, line
balancing & LTO
Management.
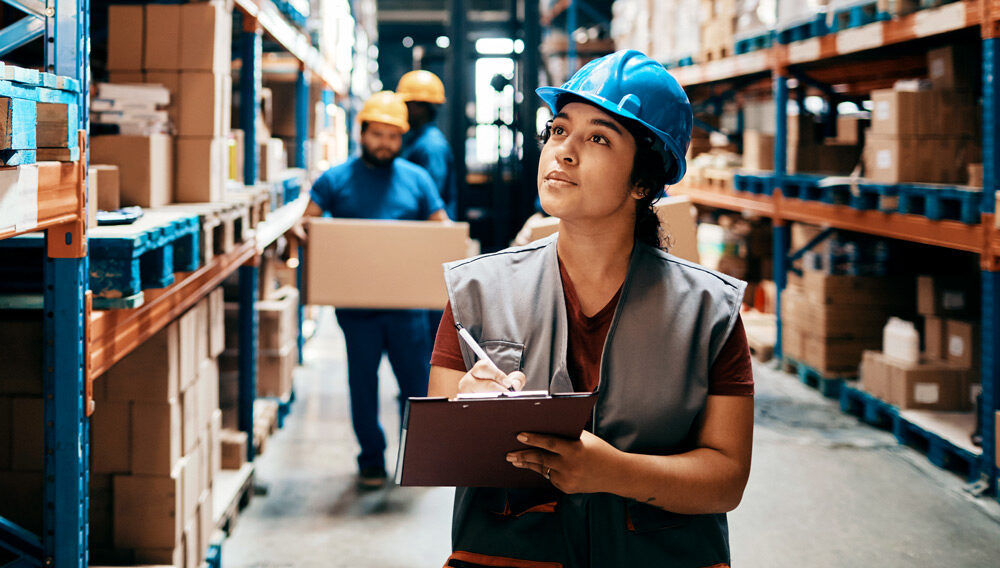
Supply Chain
Warehouse management, Stock Control & visibility,
Fabric
Quality
assurance & optimal Bin Allocation.
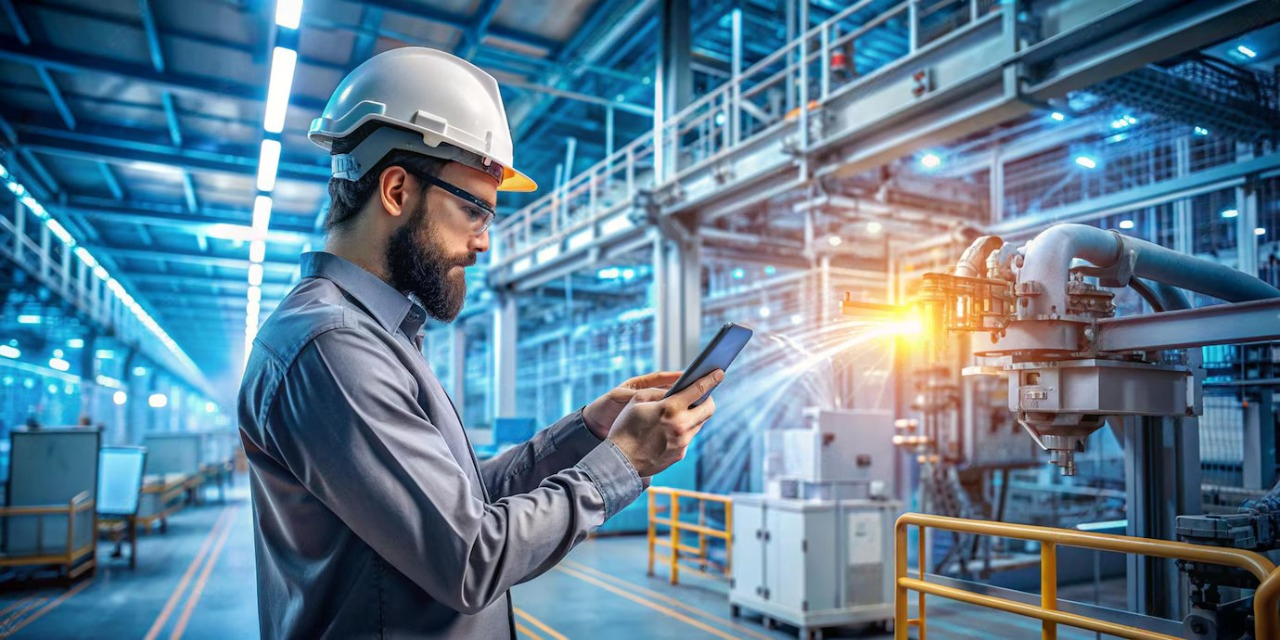
Order Book & Production Control
Auto Order Creation(BOT), Material availability(FSP) ,
Operation order
definition, FG Level Tracking, WIP Management & Downtime Capturing.
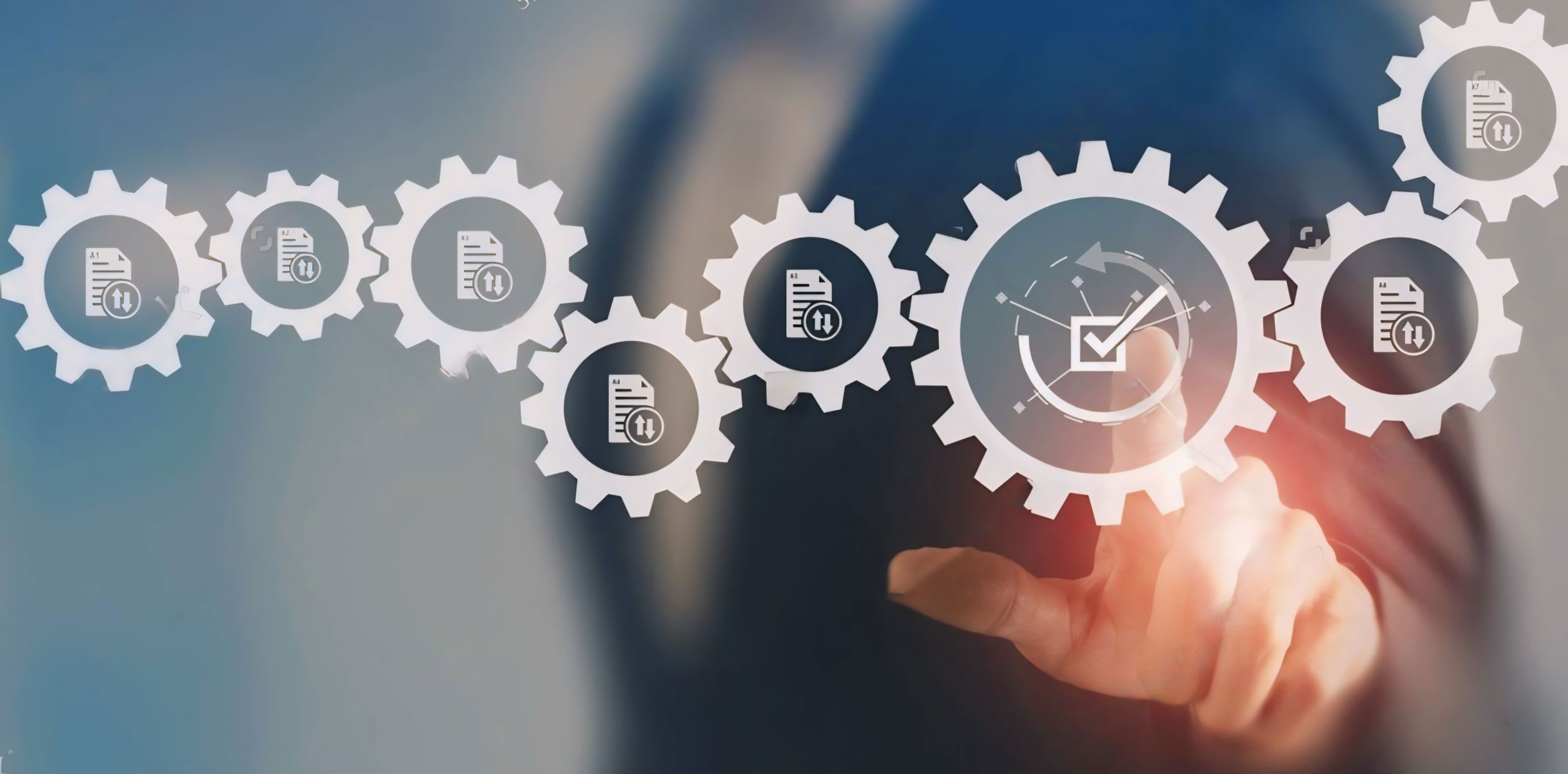
Seamless Integration
With M3, SAP, CRM, FR, Tukatech & Gerber etc...
Apparel Case Study
One of our client, a leading apparel manufacturer known for
innovative
designs and global presence, encountered difficulties managing intricate workflows and manual processes.
Inefficiencies in data entry, validation, and reporting were adversely affecting productivity, impeding the
company's agility in responding to market demands.
Lack of Integration
The client currently relies on manual methods such as
downloading Excel
files and human input to track and integrate orders from external ERP systems.
Complex Workflows
The business operates with complex workflows on the floor,
where
processes vary based on the product or styles being handled. However, there is currently no streamlined
system in place to effectively track and manage these operations.
Manual Data Entry
The client heavily relied on manual data entry processes,
resulting in
frequent errors, delays, and inefficiencies throughout their operations.
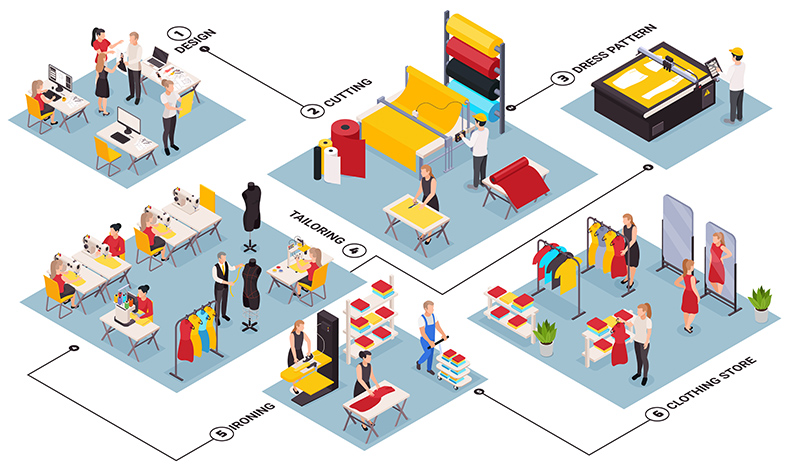
500+
100k+
2K+
1k+
Real Impact On Our Existing Customers
30
+
Locations
Cloud based management of over 30 productions in real time.
1
M+
Savings
By overcoming challenging in apparel manufacturing
10
M+
Orders
Processed through the solution
5
+
Integrations
To other main stream solutions
Key Features
Experience the future of communication with our
apparel
end-to-end solution.
Our Valued Customers


See More Products!